In the intricate world of industrial manufacturing, the distinctions between hot melt adhesive film and film are profound, each offering specialized properties and applications tailored to diverse industry needs. This comprehensive comparison will thoroughly explore the composition and structure, application methods, and extensive advantages of hot melt adhesive films, with a focus on Alster as a prominent manufacturer setting industry standards in adhesive technology.
Structure of Hot Melt Adhesive Film and Film
- Hot Melt Adhesive Films (HMAs):Hot melt adhesive films are engineered from thermoplastic polymers that are solid at room temperature and become fluid when heated above their melting point. These polymers typically include polyethylene (PE), polypropylene (PP), polyester (PET), polyamide (PA), or blends thereof, formulated with additives to enhance bonding characteristics. The films are designed to adhere to substrates through heat activation, providing strong and durable bonds upon cooling.
- The composition of HMAs ensures versatility in bonding various materials, including textiles, plastics, metals, and composites. This flexibility makes them indispensable in industries requiring reliable adhesion solutions, such as automotive assembly, electronics manufacturing, and textile lamination.
- Thin Films:Thin films encompass a broad spectrum of materials and structures, ranging from polymers and metals to ceramics and composites. These films are characterized by their uniform and often nanometer-scale thickness, deposited onto substrates using specialized techniques like physical vapor deposition (PVD), chemical vapor deposition (CVD), sputtering, or spin coating.
- Thin films serve multifaceted purposes depending on their material composition and deposition method. They are utilized in applications such as optical coatings, protective barriers, semiconductor devices, and flexible electronics. The precise control over film thickness and material properties enables tailored solutions for diverse industrial and technological applications.
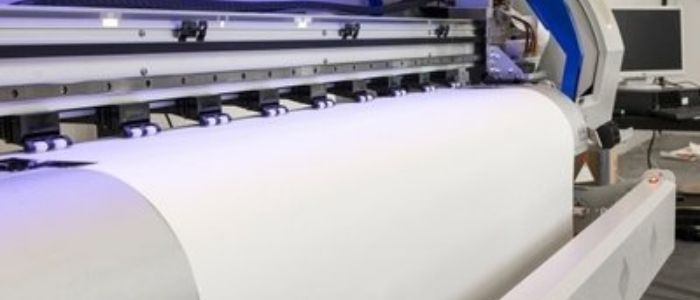
Application Methods
- Hot Melt Adhesive Films (HMAs):The application of HMAs involves the use of heat and pressure to activate and bond the adhesive to substrates. The films are supplied in rolls or sheets, which are heated to their melting point using equipment such as hot presses or heat guns. Once molten, the adhesive layer adheres to the substrate surface upon cooling, forming a strong and resilient bond.
- This method offers several advantages:
- Precision:HMAs allow for precise adhesive placement, enabling intricate bonding patterns and designs without the limitations of traditional liquid adhesives.
- Efficiency:The simplicity of the application process reduces production time and labor costs, enhancing overall manufacturing efficiency.
- Environmental Benefits:HMAs are solvent-free, eliminating volatile organic compound (VOC) emissions associated with solvent-based adhesives, thus promoting safer working environments and sustainable manufacturing practices.
- Thin Films:Thin films are deposited onto substrates using advanced deposition techniques tailored to the specific material properties and application requirements. These methods include:
- Physical Vapor Deposition (PVD):Involves vaporizing a solid material and condensing it onto a substrate, forming a thin film through processes such as evaporation or sputtering.
- Chemical Vapor Deposition (CVD):Chemical reactions are used to deposit thin films of materials onto substrates, offering precise control over film composition and structure.
- Spin Coating:Spreads a liquid precursor onto a rotating substrate, forming a uniform thin film as the solvent evaporates.
- The application methods for thin films are chosen based on factors such as substrate compatibility, film thickness requirements, and desired material properties. Thin films are critical in industries requiring precise optical, electrical, or protective coatings, where uniformity and adherence to stringent specifications are paramount.
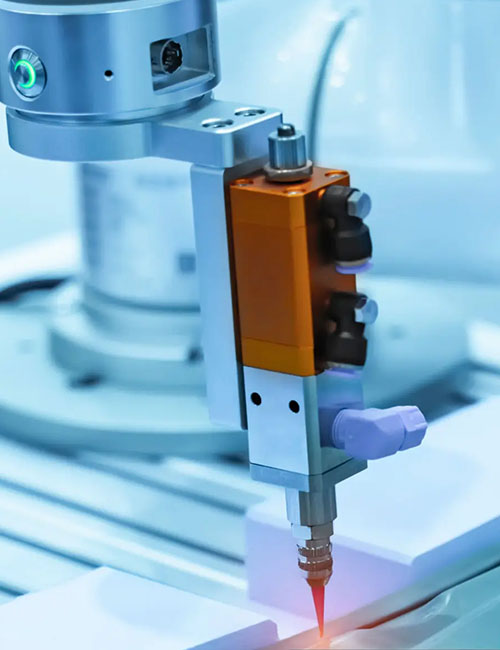
Advantages of Hot Melt Adhesive Films (HMAs)
- Versatility Across Substrates:HMAs exhibit strong adhesion to a wide range of materials, including plastics, metals, textiles, and composites. This versatility enables their use in diverse applications such as automotive assembly (for interior components and trim), textile bonding (for apparel and footwear), and electronics (for component assembly and encapsulation).
- Enhanced Durability and Performance:The bonding strength of HMAs ensures durable and resilient joints that withstand mechanical stresses, temperature fluctuations, and environmental conditions. This reliability is crucial in applications requiring long-term performance and product integrity, such as in outdoor apparel, automotive interiors, and electronic devices.
- Simplified Production Processes:HMAs streamline manufacturing processes by eliminating the need for complex mixing, curing, or cleanup associated with liquid adhesives. This simplification reduces production costs, enhances workflow efficiency, and supports high-volume manufacturing requirements.
- Environmental Sustainability:HMAs contribute to environmental sustainability by eliminating solvent emissions and reducing hazardous waste generation. Their solvent-free formulation improves workplace safety and aligns with global initiatives for sustainable manufacturing practices.
- Design Flexibility:HMAs facilitate intricate bonding patterns and designs without compromising adhesive strength. Manufacturers can achieve complex geometries and join dissimilar materials effectively, expanding design possibilities and product innovation.
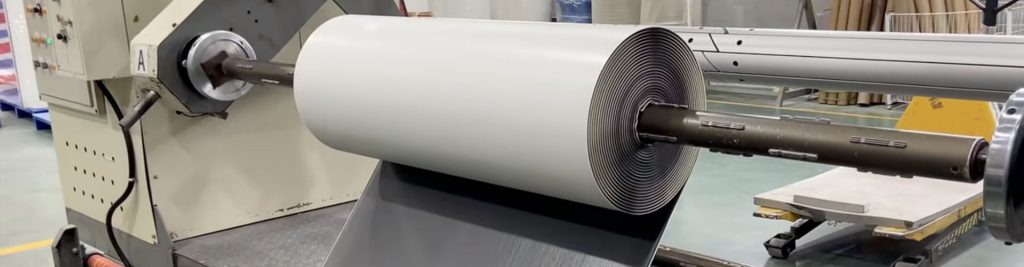
Alster: Leading the Way in Hot Melt Adhesive Films
Alster has established itself as a leader in the field of hot melt adhesive films, offering innovative solutions tailored to meet the evolving demands of global industries. The company’s commitment to excellence is reflected in:
- Product Innovation:Alster continuously develops new formulations and technologies to address specific application challenges and enhance product performance.
- Customization:Alster provides customized adhesive solutions to meet unique customer requirements, collaborating closely to optimize bonding performance and achieve superior results.
- Quality Assurance:Rigorous quality control measures ensure that each batch of adhesive films meets stringent performance standards and customer expectations.
- Technical Expertise:Alster’s dedicated technical support team offers comprehensive guidance on adhesive selection, application methods, and process optimization, empowering manufacturers to maximize efficiency and productivity.
Alster’s adhesive films are utilized across diverse industries, including automotive, electronics, textiles, and packaging, where reliability, performance, and sustainability are paramount. By partnering with Alster, manufacturers gain access to cutting-edge adhesive technologies and industry-leading expertise, driving innovation and success in their respective markets.
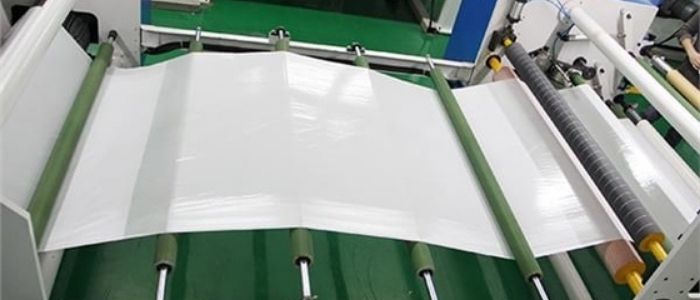
Conclusion
In conclusion, while both hot melt adhesive films and thin films play indispensable roles in modern manufacturing, their distinct compositions, application methods, and advantages cater to specific industrial needs and applications. Hot melt adhesive films offer unparalleled benefits such as versatility across substrates, enhanced durability, simplified production processes, environmental sustainability, and design flexibility. As a trusted manufacturer and innovator in adhesive technology, Alster exemplifies excellence in providing tailored solutions that optimize performance, efficiency, and sustainability across diverse manufacturing sectors. Choosing Alster ensures access to advanced adhesive technologies, expert support, and a partnership dedicated to driving continuous innovation and success in today’s competitive marketplace.