In modern industry and manufacturing processes, hot-melt adhesive film (Hot-Melt Adhesive Film) as an important adhesive material has been widely used in electronic products, automobiles, home appliances, packaging and many other fields. According to different usage requirements, hot-melt adhesive films can be divided into hot-melt adhesive film without substrate and hot-melt adhesive film with substrate.
Although both have the basic characteristics of hot-melt adhesive film – that is, they melt by heating and quickly bond the materials after cooling, there are some significant differences between them. This article will make a detailed comparison of hot-melt adhesive film without substrate and hot-melt adhesive film with substrate from several key aspects to help users make the most suitable choice according to their needs.
1. Definition and basic differences
Hot-melt adhesive film without substrate is a film-like material composed only of hot-melt adhesive, usually a single-layer or multi-layer adhesive film, without any other carrier or substrate attached. Hot-melt adhesive film without substrate can directly melt and form an adhesive layer after heating, so no additional support material is required.
In contrast, a hot melt adhesive film with a substrate has a layer of supporting material (usually plastic film, paper or other synthetic materials) attached to the hot melt adhesive film. This substrate allows the adhesive film to maintain structural stability before heating and helps the adhesive film better cover and bond the target surface during the bonding process.
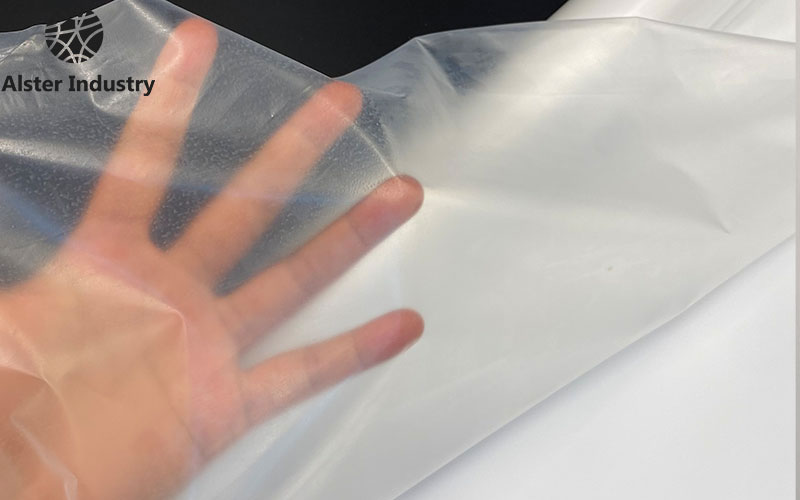
2. Bonding performance
One of the main advantages of hot melt adhesive films without substrates is their direct bonding performance. When the adhesive film is heated to its melting point, the hot melt adhesive will quickly melt and penetrate into the bonded surface. Without the interference of the substrate, the bonding effect of the hot melt adhesive film is more pure and direct, and it is suitable for occasions that require high-strength and durable bonding. For example, in the packaging of electronic components, hot melt adhesive films without substrates can provide better sealing and high temperature resistance.
Hot melt adhesive films with substrates are usually used in applications with lower surface bonding requirements. The substrate can alleviate the melting speed and bonding strength of the hot melt adhesive to a certain extent, which makes it perform better in processes that require extended processing time or avoid premature curing. The substrate can also ensure that the film has sufficient stability before melting. In some complex or irregular bonding occasions, the hot melt adhesive film with substrate can provide better operability and stability.
3. Processing convenience and application scope
The hot melt adhesive film without substrate is usually easier to process, especially for high-precision applications. For example, in the packaging of film layers or the packaging of precision components of electronic products, the hot melt adhesive film without substrate can be directly melted and adapted to different design forms because there is no substrate. This makes the hot melt adhesive film without substrate particularly suitable for small batches, high precision and high-demand processes.
However, the hot melt adhesive film without substrate also has certain limitations during processing. For example, it is easy to stretch or deform during operation, and requires higher precision requirements in temperature and pressure control. In addition, the bonding surface requirements of the hot melt adhesive film without substrate are higher, and it cannot adapt to more complex surface morphology like the hot melt adhesive film with substrate.
The hot melt adhesive film with substrate makes the processing process more stable and controllable due to the presence of the substrate. The support of the substrate makes the film less likely to deform irregularly when heated, and is suitable for some processes that require high structural strength. At the same time, the substrate can better adapt to the bonding of different materials and surfaces, and is widely used in the bonding of larger or heavier objects, such as the automotive industry, home appliance manufacturing, etc.
The processing of hot melt adhesive films with substrates is also more flexible, and the substrate can be customized according to needs, making it more widely used in different fields, so as to meet different production needs.
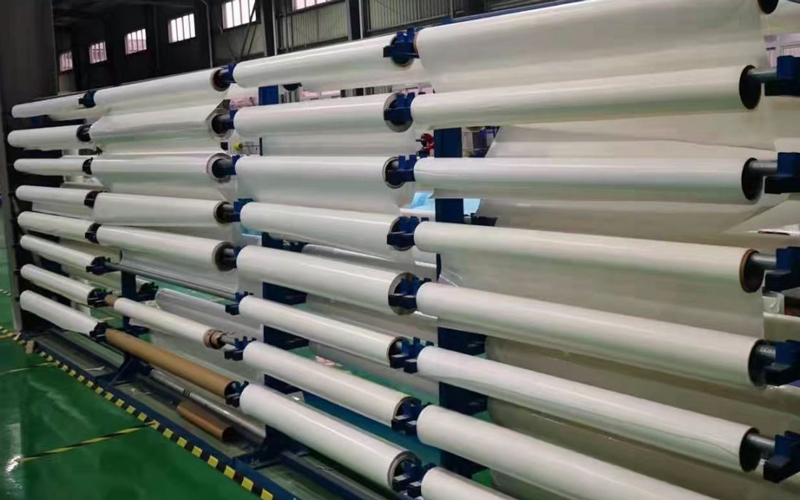
4. Thermal stability and durability
The hot melt adhesive film without substrate usually has good thermal stability due to its simple structure. The design without substrate makes it difficult for the adhesive film to separate from the substrate and the adhesive layer during heating, providing a more uniform melting effect. Therefore, it is usually more durable in high temperature or high load working environments. The durability of hot melt adhesive films without substrates is particularly suitable for fields that require long-term bonding strength.
However, due to the lack of substrate support, some hot melt adhesive films without substrates may soften and degrade under extreme temperature and humidity conditions. Therefore, in applications with large environmental changes, the heat resistance and aging resistance of the film need to be considered in detail.
Hot melt adhesive films with substrates are slightly inferior in durability, but the addition of substrates makes them stable enough for most industrial applications. The substrate not only improves the overall strength of the film, but also enhances its adaptability in some extreme environments. For example, some hot melt adhesive films with substrates can maintain good flexibility in low temperature environments, so they are better used in cold areas.
5. Cost and environmental considerations
Hot melt adhesive films without substrates are usually cheaper to manufacture due to their simple materials. Especially in high-end applications, the cost advantage of pure hot melt adhesive films makes hot melt adhesive films without substrates an economical and practical choice. However, with the increase in high-performance requirements, the special formulations of some hot melt adhesive films without substrates may increase their overall cost.
The cost of hot melt adhesive films with substrates is usually higher because the addition of substrate materials and the complexity of the production process increase the overall manufacturing cost. However, the versatility and wider application range of hot melt adhesive films with substrates make it a more cost-effective choice in some large-scale production.
In terms of environmental protection, many hot melt adhesive films with substrates use recyclable and degradable substrates, which helps to improve their environmental performance. Relatively speaking, some hot melt adhesive films without substrates may not be easy to recycle or decompose, and special attention should be paid to their environmental impact.
Summary
Hot melt adhesive films without substrates and hot melt adhesive films with substrates each have unique advantages and applicable occasions. Hot melt adhesive films without substrates are suitable for high-precision and small-batch applications due to their simple processing methods and high bonding strength, while hot melt adhesive films with substrates are ideal for large-scale production and complex shape bonding due to their higher stability and adaptability.
The key to choosing which hot melt adhesive film lies in the specific application requirements, including temperature, humidity, bonding strength requirements, processing methods and other factors. By comprehensively considering these factors, users can make the best choice between the two to achieve more efficient, economical and compliant production results.