Seamless underwear is widely welcomed by the market for its comfort, fit and beauty, and seamless bras are particularly favored by consumers. Silicone brushing machines (silicone coating machines) play a vital role in the production process of seamless bras, and can achieve functions such as anti-slip, shaping and enhanced fit. So, how is the silicone brushing machine used in the manufacture of seamless bras? This article will introduce the entire process and its advantages in detail.
1. Characteristics of seamless bras and the importance of silicone coating
Seamless bras use seamless fitting technology to avoid the steel rings and stitches of traditional bras, bringing better comfort. Silicone coating technology is mainly used for shoulder straps, underbands and cups to make them more stable, fit and non-slip, and improve the wearing experience.
The functions of silicone brushing machines include:
- Enhance anti-slip performance-by evenly coating silicone on shoulder straps, underbands and other parts, the bra is not easy to slip.
- Improve shaping effect-apply silicone dots or strips on the cups or underbands to enhance support and shape a more perfect chest line.
- Improve durability – Silicone has good washing and abrasion resistance, which can extend the service life of bras.
- Add fashion elements – Customizable silicone patterns, such as stripes, waves, LOGO, etc., can add a sense of design to bras.
2. The process flow of silicone brushing machine in seamless bra production
1. Design and cutting
Before producing seamless bras, you first need to design the shape and size of the product. Seamless underwear is usually made of elastic fabrics (such as nylon and spandex), and is precisely cut by laser cutting or ultrasonic cutting to avoid the bulges and friction caused by traditional sewing methods.
2. Pretreatment (cloth cleaning and fixing)
Before silicone coating, the fabric needs to be cleaned and fixed to ensure that the silicone can be evenly attached without affecting the adhesion effect. This usually includes removing dust and oil from the surface and fixing the fabric on the workbench of the silicone brushing machine with a clamp or mold.
3. Silicone blending
Silicone is usually a two-component liquid silicone. Before use, it needs to be mixed in a certain proportion and an appropriate amount of catalyst is added to ensure that the silicone can be evenly cured. According to the design requirements of the bra, you can choose transparent silicone, colored silicone or silicone with textured effects.
4. Silicone brush coating
Silicone brush machines (such as AT-B01 silicone coating machines) achieve uniform and stable silicone coating through precise control. The main coating methods include:
- Point coating: suitable for anti-slip areas, such as shoulder straps, inside the cup, etc.
- Strip coating: used for the lower part of the waist, to strengthen support and increase stability.
- Full-surface coating: Cover a layer of silicone in a specific area to improve fit.
The advantages of silicone brush machines are:
The thickness of the silicone can be accurately controlled to avoid the effect of too thick or too thin coating.
Applicable to different pattern customization, such as anti-slip strips, wavy patterns, brand LOGO, etc.
Through automated operation, improve production efficiency and reduce manual errors.
5. Drying and curing
After the silicone coating is completed, it needs to be cured to make it firmly attached to the fabric. Usually, heating and drying are used to make the silicone cure quickly at a temperature of 120-150°C to ensure that it is washable, wear-resistant and not easy to fall off.
6. Seamless bonding and shaping
After the silicone is cured, the bra is then spliced and shaped. Since seamless bras do not use traditional sewing technology, they are seamlessly bonded by heat pressing, ultrasonic welding or hot melt adhesive film (such as LQ361T hot melt adhesive film) to ensure overall softness and comfort.
7. Quality inspection and packaging
After production, the bras need to be quality inspected, including:
- Silicone adhesion firmness test
- Anti-slip effect test
- Washable and wear-resistant test
- Wearing comfort test
- Qualified products can be shipped after sorting, folding and packaging.
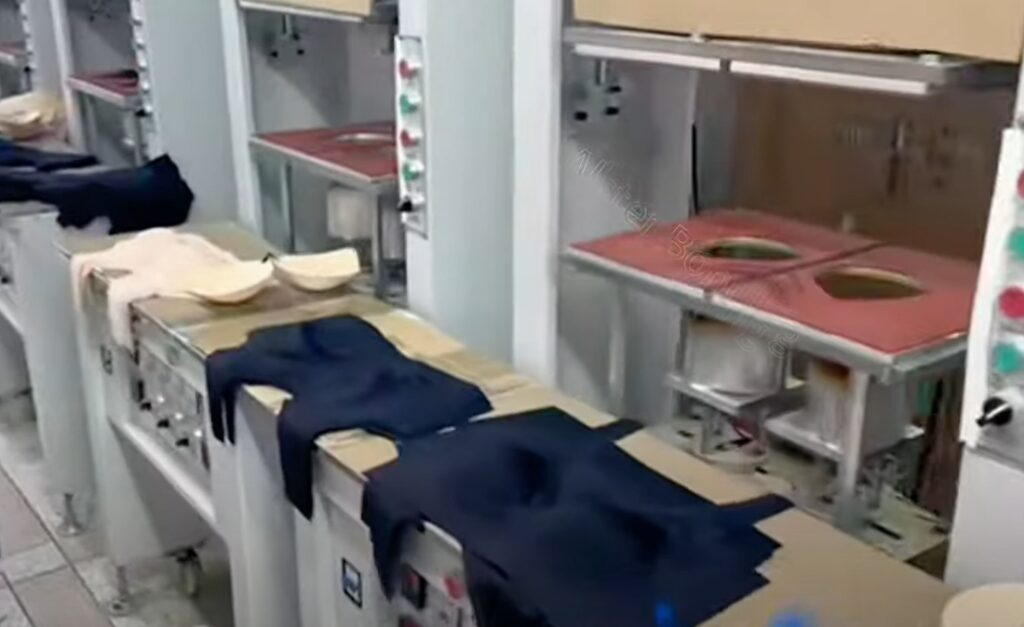
3. Advantages of silicone brushing machine in seamless bras
Using silicone brushing machine for coating not only improves the quality of seamless bras, but also improves production efficiency. Its main advantages include:
- High-precision coating-silicone brushing machine can accurately control the coating area and thickness to ensure product consistency.
- Production automation-compared with manual brushing, silicone brushing machine can increase production and reduce labor costs.
- Diversified design-supports customization of different patterns and colors to meet personalized market needs.
- Environmentally friendly materials-using non-toxic and odorless liquid silicone, in line with international environmental standards.
- Enhance market competitiveness-anti-slip, shaping, wear-resistant and other functions make seamless bras more attractive and improve brand competitiveness.
4. Summary
Silicone brushing machines made by Alster play an important role in the manufacture of seamless bras. Through high-precision coating technology, bras have better anti-slip, support and comfort performance. From cutting, coating, curing to final shaping, each step affects the quality and performance of the product. With the continuous development of the seamless underwear market, silicone coating technology will continue to be optimized to provide consumers with more comfortable and fashionable seamless bra products.
For seamless bra manufacturers, the use of advanced silicone brushing machines can not only improve product quality, but also optimize production processes and meet the market demand for high-end underwear. Therefore, investing in efficient silicone coating equipment is undoubtedly an important strategy to enhance brand competitiveness.