As a hot melt adhesive product widely used in various industries, TPU hot melt adhesive film has been favored by many fields due to its excellent performance. TPU hot melt adhesive film is not only widely used in the clothing industry and the automotive industry, but also performs well in electronics, batteries, packaging and other fields. So, how is TPU hot melt adhesive film produced? This article will introduce the production equipment, production methods and production line composition of TPU hot melt adhesive film in detail to help you better understand its production process.
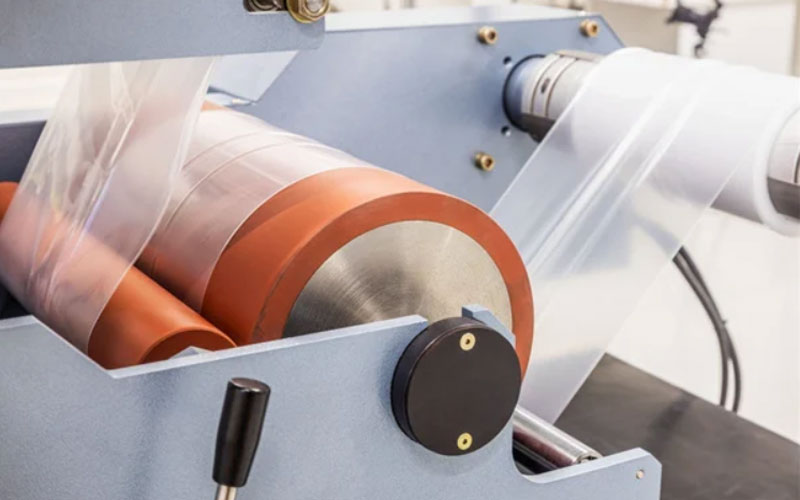
Equipment required for the production of TPU hot melt adhesive film
The production of TPU hot melt adhesive film requires a complete set of advanced equipment, and the cooperation of these equipment can ensure the production of high-quality TPU hot melt adhesive film. Although the equipment of the production line is not complicated from the outside, each equipment plays a vital role in the production process. Generally speaking, the main equipment of TPU hot melt adhesive film production line includes the following 12 types:
- Single screw extruder: Single screw extruder is one of the core equipment for the production of TPU hot melt adhesive film. It is used to heat and melt TPU particles and extrude them through a mold.
- Hydraulic screen changer: The hydraulic screen changer is used to filter impurities during the production process to ensure the purity of the molten TPU colloid and avoid defective products in the subsequent production process.
- Metering pump: The metering pump is used to accurately control the flow rate of the TPU melt to ensure the uniformity of the colloid amount during each production.
- Mold: The mold is a key tool for pressing the melt into the desired shape. The precision and design of the mold directly affect the quality of the TPU hot melt adhesive film.
- Laminating device: The laminating device is used to compound the molten TPU with the release paper to protect the surface of the TPU film.
- Calender: The calender is used to calender the hot melt adhesive film to ensure that the surface of the film is flat and achieve a higher gloss and visual effect.
- Roller temperature control system: The roller temperature control system is used to adjust the temperature of the roller to ensure the stability of the temperature during the production process and avoid deformation or unevenness of the adhesive film.
- Cooling bracket, trimming device: The cooling bracket is used to help the hot melt adhesive film cool down, and the trimming device is used to remove the edge of the film to ensure that the size of the film meets the requirements.
- Tractor, waste edge winding device: The tractor is used to haul the TPU hot melt adhesive film, and the film is rolled out by traction, and it cooperates with the waste edge winding device to collect and process the waste edges generated during the production process.
- Double-station winding machine: The double-station winding machine is used to roll the produced TPU hot melt adhesive film into rolls, and can achieve continuous production to avoid downtime and waiting.
- Full set of electrical control systems: The full set of electrical control systems is the “brain” of the production line. It is responsible for coordinating the operation of all equipment to ensure the efficiency and stability of the production process.
- Auxiliary equipment: Auxiliary equipment includes cooling systems, automatic packaging equipment, etc., to ensure that all links in the production process are carried out smoothly.
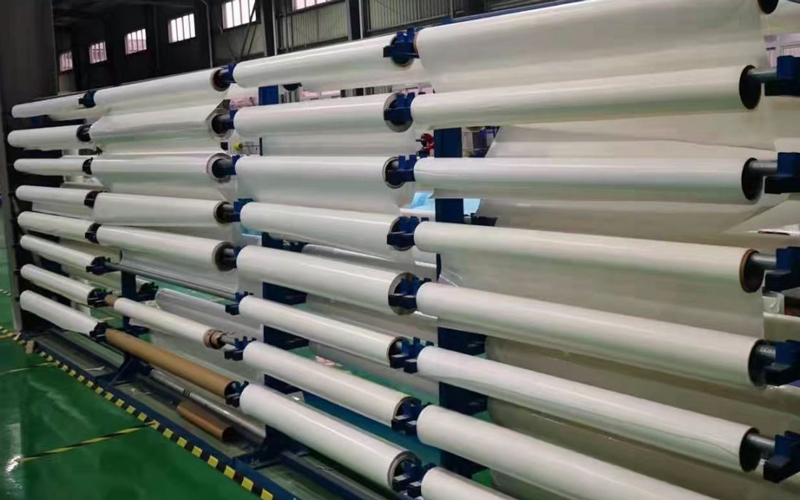
Production method of TPU hot melt adhesive film
There are usually two methods for producing TPU hot melt adhesive film, namely “release paper protection method” and “Teflon roller method”. These two methods have their own advantages and disadvantages. In actual applications, they are selected according to production needs and costs.
1. Release paper protection method
The release paper protection method is a commonly used production method. First, after the molten body is extruded through the die, it is sandwiched between two layers of release paper. These two layers of release paper play a protective role, preventing the TPU molten body from contacting other surfaces and avoiding adhesion. Then, it is pressed into a film through a forming roller, and the final TPU hot melt adhesive film can be obtained after cooling. The advantage of this method is that it can avoid surface defects and ensure the integrity of the film surface. However, the use of two layers of release paper will cause a certain waste of resources.
2. Teflon roller method
Another production method is to use a forming roller coated with Teflon. Teflon has excellent high temperature resistance and non-stick properties, so it can prevent the molten TPU from sticking to the forming roller. The disadvantage of this method is that during the production process, the Teflon roller and the molten TPU occasionally stick together, resulting in bubbles and defects on the surface, affecting the quality of the film. In addition, as production proceeds, the Teflon layer will gradually lose its effect due to wear and tear, and it needs to be re-plated with Teflon regularly, which increases production costs.
Therefore, the release paper protection method is currently a more common and economical production method, especially suitable for large-scale production.
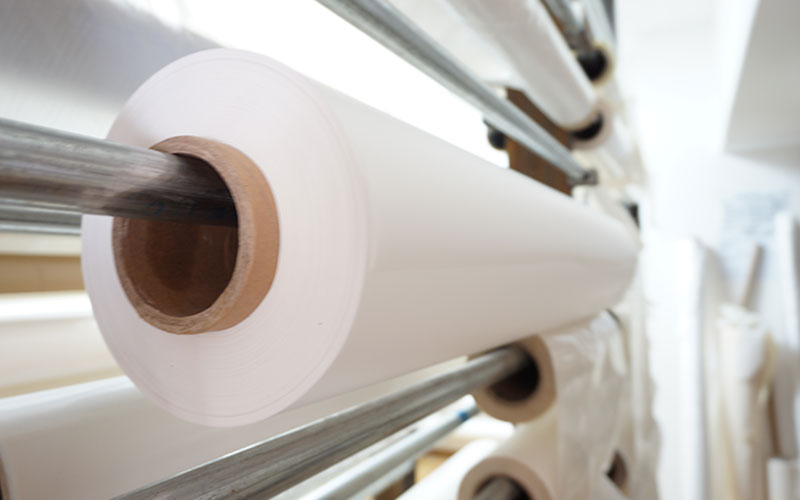
Key elements of TPU hot melt adhesive film production
The production of TPU hot melt adhesive film requires not only advanced equipment and precise production processes, but also the control of the following key elements to ensure the quality of the final product:
- Temperature control: In the production process, the control of melting temperature is crucial. Too high temperature may cause the TPU material to decompose, and too low temperature may cause poor material fluidity and affect the molding effect.
- Roller temperature control: Roller temperature directly affects the thickness uniformity and surface smoothness of the film. Accurate roller temperature control can effectively ensure product quality.
- Cooling system: Cooling speed and cooling method directly affect the hardness and compressive strength of the film. Generally, a slower cooling process helps to form a tougher film.
- Film thickness control: By accurately controlling the extrusion amount and roller pressure strength, the thickness of the TPU hot melt adhesive film can be adjusted to ensure the uniformity and stability of the film.
Conclusion
The production of TPU hot melt adhesive film is a highly sophisticated process involving the coordination of multiple links and equipment. By reasonably selecting production methods and finely controlling production factors, the quality of the product can be effectively improved. For customers, choosing a suitable manufacturer not only depends on its production capacity, but also on the maturity of its equipment configuration and production process. Ultimately, choosing TPU hot melt adhesive film products with stable quality, no bubbles, and uniform thickness can meet the needs of different application fields.