In the ever-evolving world of garment manufacturing, efficiency, precision, and aesthetics go hand in hand. One of the latest innovations being adopted by high-end garment manufacturers is the ultrasonic punching machine, especially for creating seamless POLO shirt plackets. Unlike traditional sewing methods, ultrasonic technology offers a clean, durable, and elegant finish without needle and thread, making it an ideal solution for performance wear, casual fashion, and premium clothing lines.
This article provides a comprehensive guide on how to make a seamless POLO shirt placket using an ultrasonic punching machine, including equipment overview, material selection, step-by-step procedures, benefits, and key considerations.
1. Understanding Ultrasonic Punching Technology
Ultrasonic punching uses high-frequency mechanical vibrations (typically 20kHz or higher) to generate heat through friction. This heat melts synthetic fibers at the molecular level, allowing for bonding, cutting, or punching without traditional stitching.
The core components of an ultrasonic punching system include:
- Ultrasonic Generator – Converts electrical energy into high-frequency signals.
- Transducer – Converts electrical signals into mechanical vibrations.
- Booster and Horn (Sonotrode) – Amplify and direct the vibrations to the material.
- Punching Mold – Customized die shapes used to cut or bond fabric.
For garment plackets, the mold is tailored to create sharp edges, clean openings, or reinforced areas where buttons or snaps may be placed.
2. Why Use Ultrasonic for Seamless Plackets?
Traditional plackets are created by folding and stitching fabric layers. This process, though reliable, has some limitations:
- Visible seam lines.
- Bulk in the front panel.
- Time-consuming process.
- Needle holes may weaken certain synthetic fabrics.
Ultrasonic punching eliminates these concerns:
- Seamless finish – No stitches or threads.
- High speed – Automated bonding and punching in one step.
- Stronger bond – Especially for synthetic blends.
- Aesthetic quality – Smooth, clean appearance.
3. Suitable Materials for Ultrasonic Placket Making
Ultrasonic technology works best with thermoplastic synthetic fibers. The heat generated by vibration melts the fibers slightly, allowing them to fuse under pressure.
Ideal fabrics include:
- 100% Polyester
- Polyester blends (e.g., poly-cotton)
- Nylon
- Spandex or Lycra blends
Note: Natural fibers like 100% cotton or linen do not respond well unless blended with synthetic materials.
4. Preparation Before Punching
a. Design the Placket Area
Design the POLO shirt pattern with a placket region marked for ultrasonic processing. The shape and size should match the customized ultrasonic mold.
b. Fabric Conditioning
Ensure the fabric is:
- Clean and wrinkle-free.
- Pre-shrunk (if necessary).
- Aligned correctly with the machine to prevent off-center punching.
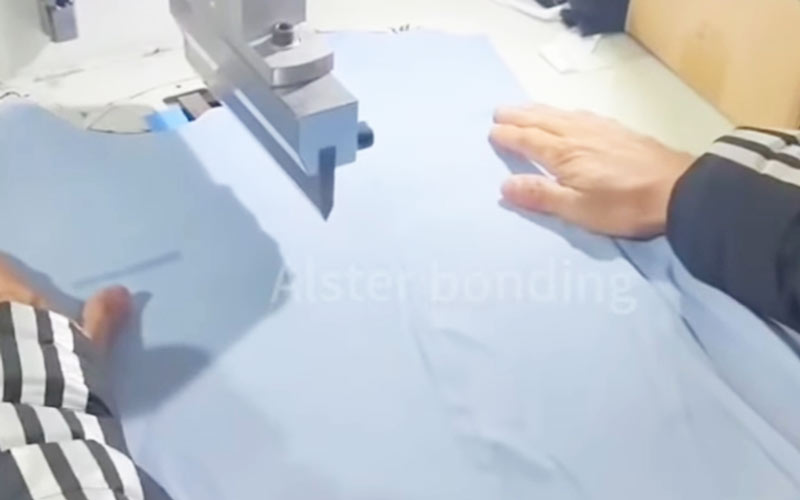
5. Step-by-Step Process: Making a Seamless POLO Placket
Step 1: Set Up the Ultrasonic Punching Machine
- Install the placket-specific mold into the machine.
- Adjust the horn pressure, frequency, and welding time according to material thickness and type.
- Perform test runs with scrap fabric for calibration.
Step 2: Align the Fabric
- Place the shirt front panel on the working platform.
- Align the marked placket region under the horn.
- Secure the fabric in place using clamps or vacuum suction if available.
Step 3: Initiate Ultrasonic Punching
- Activate the machine.
- The horn vibrates at high frequency, heating and punching the fabric in a single pass.
- The result: a neat, bonded placket slit with clean edges and optional buttonhole shapes, depending on the mold design.
Step 4: Final Finishing (Optional)
- Add buttons using heat-press or snap tools.
- Optionally reinforce the backside with a bonded synthetic patch.
- Conduct quality inspection for strength, cleanliness, and alignment.
6. Advantages of Seamless Ultrasonic Plackets
Feature | Ultrasonic Seamless Placket | Traditional Sewn Placket |
---|---|---|
Aesthetic | Smooth, modern, minimal | Visible stitches |
Comfort | No internal seam bulk | May irritate skin if bulky |
Production Speed | Faster with automation | Slower, labor-intensive |
Fabric Compatibility | Ideal for synthetics | Works with all, but slower |
Durability | Excellent for activewear | Depends on thread and stitching |
Would you like more details on specific machine models or troubleshooting tips? Or Are you looking for machines? Welcome to contact Alster!
7. Limitations and Considerations
While ultrasonic punching machine offers many advantages, there are also important limitations to be aware of:
- Material Dependency: Pure natural fibers don’t work well; blends are required.
- Initial Investment: Ultrasonic machines and molds can be expensive.
- Design Constraints: Only suitable for designs that can be accommodated by the punching mold.
- Customization Required: Each placket shape may need a new mold, increasing tooling costs.
8. Maintenance and Quality Control
Maintenance Tips:
- Regularly clean the horn and mold to prevent fiber buildup.
- Check for alignment of the horn and anvil.
- Monitor generator output frequency and power.
Quality Checks:
- Ensure uniform bonding and punching.
- Test tear strength of placket region.
- Verify alignment and shape consistency.
9. Applications Beyond POLO Shirts
Ultrasonic punching isn’t limited to POLO shirts. It’s also widely used in:
- Seamless sportswear and activewear
- Underwear and lingerie
- Nonwoven medical garments
- Waterproof apparel
- Synthetic fashion wear
10. Conclusion
Ultrasonic punching technology is revolutionizing the way we manufacture seamless plackets for POLO shirts and other garments. By leveraging high-frequency vibrations, this method not only speeds up production but also ensures a refined, comfortable, and modern finish. While it does require upfront investment and proper material selection, the long-term benefits for high-quality synthetic garment production are undeniable.
As consumer expectations rise and minimalist aesthetics become mainstream, seamless POLO shirt plackets made with ultrasonic punching machines that are manufactured by Alster may soon become the new standard in premium apparel manufacturing.