The textile and apparel industry has undergone significant advancements in recent years, with seamless garment manufacturing emerging as a game-changer. Consumers today demand clothing that not only looks good but also provides superior comfort, flexibility, and durability. Traditional sewing methods often fail to meet these requirements, as the presence of stitches can create bulkiness, discomfort, and potential wear-and-tear over time.
This is where ultrasonic bonding machines come into play. These machines utilize high-frequency ultrasonic vibrations to create strong, flexible, and seamless garment constructions without the need for needles, threads, or adhesives. The ultrasonic bonding technique has revolutionized the way seamless garments are produced, providing an efficient and eco-friendly solution for manufacturers looking to enhance garment quality and production efficiency.
In this article, we will explore how ultrasonic bonding machines work, their advantages, applications in the garment industry, key factors to consider when choosing a machine, and their future potential in the textile sector.
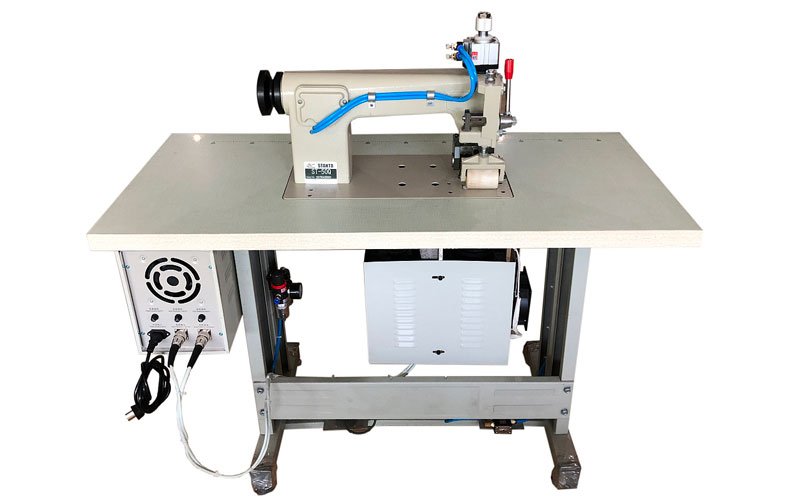
How Ultrasonic Bonding Machines Work
Ultrasonic bonding is a cutting-edge technology that leverages high-frequency sound waves to generate heat, which in turn fuses fabric layers together. This process is especially effective for thermoplastic materials, such as polyester, nylon, polypropylene, and other synthetic textiles, as they soften and bond at high temperatures without the need for additional adhesives.
Key Components of an Ultrasonic Bonding Machine
An ultrasonic bonding machine consists of several crucial components, each playing a vital role in the bonding process:
Ultrasonic Generator – Converts electrical energy into high-frequency mechanical vibrations.
Transducer – Converts electrical signals into ultrasonic vibrations that facilitate the bonding process.
Booster and Horn – Amplifies and directs the ultrasonic vibrations onto the fabric layers.
Anvil and Fixture – Applies the necessary pressure to ensure effective bonding.
Bonding Process
Fabric Placement: The fabric layers to be bonded are placed between the horn and anvil.
Ultrasonic Activation: The machine generates high-frequency ultrasonic waves that create molecular friction between the fabric layers.
Localized Heating: The friction produces heat, causing the thermoplastic fibers to melt and fuse together.
Cooling and Solidification: The fused fabric cools down quickly, forming a seamless and durable bond.
The entire process happens within fractions of a second, making it a highly efficient alternative to traditional sewing.
Advantages of Ultrasonic Bonding in Seamless Garment Production
The adoption of ultrasonic bonding technology offers numerous advantages for garment manufacturers. Below are some of the key benefits:
1. Enhanced Comfort
Traditional sewing techniques involve stitches that can create irritation, especially for sensitive areas of the body. Ultrasonic bonding eliminates stitches, making garments smooth, irritation-free, and more comfortable to wear.
2. High Durability
Seamless garments bonded using ultrasonic technology are highly durable and resistant to fraying. Since there are no threads involved, there is no risk of loose stitches or fabric unraveling after multiple washes.
3. Improved Aesthetics
Garments made with ultrasonic bonding lack visible stitches, giving them a sleek, modern, and premium look. This is particularly beneficial for high-end fashion, activewear, and lingerie.
4. Eco-Friendly Process
Unlike traditional sewing, ultrasonic bonding does not require additional consumables such as thread, glue, or chemicals, reducing textile waste and environmental impact. It is a more sustainable approach to garment manufacturing.
5. Increased Production Efficiency
The ultrasonic bonding process is faster than traditional sewing, allowing manufacturers to increase productivity while maintaining quality. Since the process is automated, labor costs are also significantly reduced.
6. Water and Air-Tight Sealing
Ultrasonic bonding creates waterproof and airtight seams, making it ideal for applications such as swimwear, raincoats, medical textiles, and protective clothing.
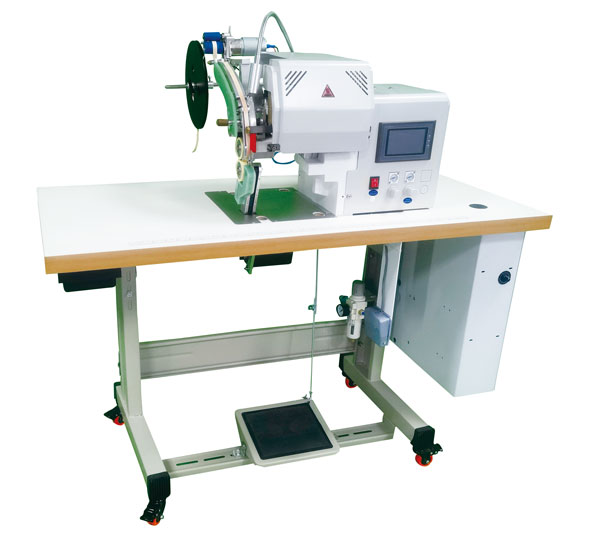
Applications in the Garment Industry
Ultrasonic bonding machines have found extensive applications across various garment segments, including:
1. Activewear and Sportswear
Seamless bonding enhances flexibility and stretchability, allowing greater freedom of movement.
No irritation from stitches, making activewear more comfortable for prolonged use.
2. Lingerie and Underwear
Delicate fabrics can be seamlessly bonded without damage.
Smooth and soft edges for ultimate skin comfort.
3. Medical and Hygiene Textiles
Used in disposable surgical gowns, face masks, protective clothing, and bandages.
Ultrasonic sealing ensures hygienic and contamination-free garments.
4. Swimwear and Waterproof Clothing
Water-resistant bonded seams eliminate the need for traditional stitching.
Enhanced durability against chlorine and saltwater exposure.
5. Industrial and Protective Wear
Workwear and safety garments require strong, durable, and seamless bonds to withstand extreme conditions.
Fire-retardant and waterproof fabrics can be effectively bonded.
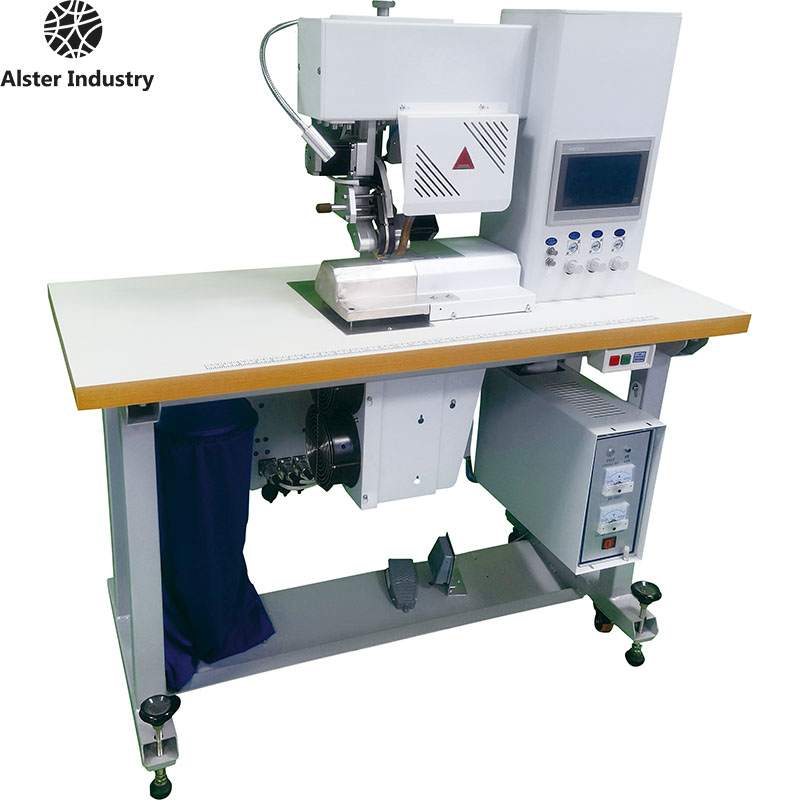
Choosing the Right Ultrasonic Bonding Machine
When investing in an ultrasonic bonding machine for seamless garment production, manufacturers must consider the following factors:
1. Material Compatibility
The machine should be optimized for thermoplastic-based fabrics such as polyester, nylon, and polypropylene.
2. Power and Frequency Adjustability
Machines with adjustable power and frequency settings provide greater flexibility for bonding different fabric thicknesses and compositions.
3. Automation and Speed
High-speed machines with automation features (such as robotic arms and conveyor systems) can significantly improve productivity and reduce labor costs.
4. Bonding Strength and Quality
Look for machines that provide consistent bonding strength without causing fabric distortion or damage.
5. Ease of Use and Maintenance
A user-friendly interface, minimal maintenance requirements, and readily available spare parts ensure smooth and efficient operation.
Future of Ultrasonic Bonding in the Textile Industry
As the demand for sustainable, high-quality, and comfortable clothing continues to rise, ultrasonic bonding technology is expected to play an even greater role in textile manufacturing. Future advancements may include:
Integration with Smart Fabrics: Bonding technology that works seamlessly with wearable tech and electronic textiles.
AI and Automation: Machines with AI-powered precision control for automated defect detection and real-time adjustments.
Expanded Material Compatibility: New developments in ultrasonic bonding may enable bonding of non-thermoplastic natural fabrics.
Conclusion
Ultrasonic bonding machines are transforming the seamless garment industry by offering a faster, more durable, and eco-friendly alternative to traditional sewing methods. From activewear and lingerie to medical textiles and swimwear, this technology is redefining garment construction.
For manufacturers looking to enhance product quality, improve efficiency, and adopt sustainable practices, investing in ultrasonic bonding technology is a strategic and forward-thinking decision. As the industry moves toward more seamless, high-performance garments, ultrasonic bonding is set to become an essential tool in modern textile production. Want to get more about these machines? Welcome to contact Alster.